MECARING seals the deal – 40 years of automated sealing of plastic pipe fittings
Paavo Laaksonen has journeyed alongside Extron MECARING since the beginning of its development. Paavo, who is now officially retired, still does occasional data transfer and consulting work, as well as managing long-term customer relationships. He has seen the growth of not only MECARING and Extron, but also the entire plastics and sealants industry.
MECARING was developed in the mid-1980s at Mecanor-Engineering Oy, which was set up by current Uponor specifically for the manufacture of new equipment. Paavo, who previously worked in maintenance, started as a sales manager and then became a production manager. In 1992, Paavo and his partners bought a subsidiary for themselves. Paavo was the company’s CEO until it was sold in 2015.
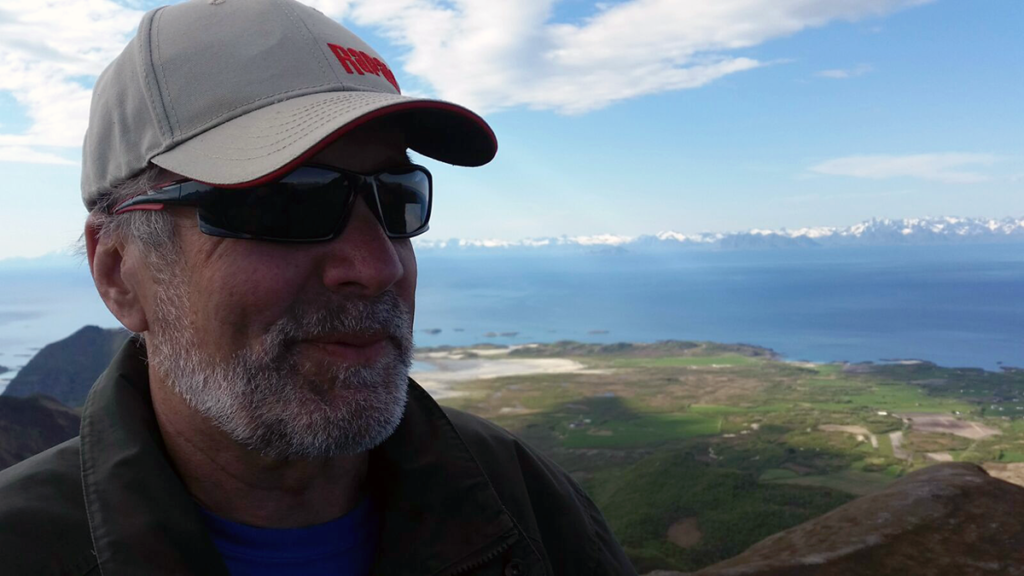
Developed to meet demand
Upo Plastic Division (current Uponor) was a pioneer in the manufacture of plastic pipes and fittings from the 1960s, both in Finland and in Europe. In the transition from fixed joints of pipes to sealing pipes, new means were required to speed up the process. The popularity and demand for plastics piping continued to grow, and the manual installation of seals brought an extra step into the process.
As volumes increased, the plastics industry began to pay more attention to labor costs. Manpower began to be replaced by conveyors that collected pipes into the packing area. We had the idea that the installation of seals would be much more efficient with a device designed for that purpose. That’s where the product development started, Paavo recalls.
The first MECARING was a simple tool that reduced the diameter of the seal and then fit into the groove inside the pipe socket. The main innovation was a shrinking nylon piston and a fixed cone that pushed the shrunken seal into the groove.
Continuous improvement
According to Paavo, the development of seals has largely dictated the development of MECARING. The challenges in the industry always determine what kind of solutions are needed from the tool designers.
The cooperation with the seal manufacturers has been very important to us. They have turned to us whenever a new type of seal has entered the market. Especially for the first 20 years, we worked closely with the world’s two largest seal manufacturers in both Europe and America, Paavo recalls.
Another major change has been the installation of seals on the outer surface of the pipe.
For corrugated pipes, the sealing groove is automatically created during pipe production. In this case, the seal must be spread open instead of shrinking. The volumes for these units are smaller than in the market for regular seals, but the prices and requirements are more significant, Paavo says.
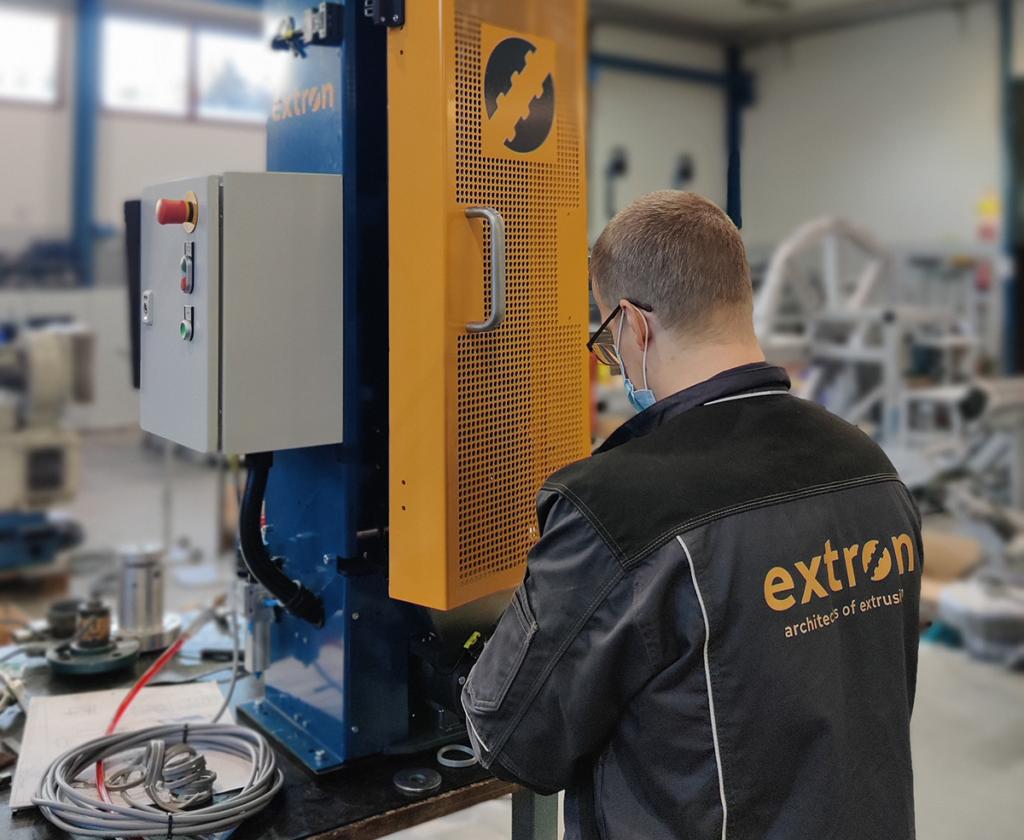
In addition to seals, the design work has been influenced by the development of automation and modern efficiency and safety requirements. As industrial labor costs rose, automation entered the arena. The robot picked the pipe directly from the mold, took it to the MECARING and then to the quality assurance point and for packaging. The need for efficiency increased, and it was important that the machine installed the seals correctly. Once the shipment was packaged, the supervisors wanted to be sure that the seals were in their grooves and the products were of high quality. At that point, safe and reliable seal installation became an even more critical part of the process.
The importance of add-on equipment is also constantly growing, and the speed of processing and packaging must also be optimized. The requirements for machine safety have also had a significant impact on MECARING’s development work. Every unit is designed to be as safe as possible, without the need to protect them from the outside.
Ready for the challenge
Extron MECARING is already known all over the world. Collaborative networks have grown, and seal manufacturers are also recommending equipment to their partners. Paavo remembers how the device was first presented internationally at the German K Show trade fair in the late 1980s.
When we re-entered in the late ‘90s, we had a robot at our showroom picking products to the sealing machine. Those events were important showcases for creating international relations, Paavo says.
The global feedback has been positive. Above all, customer satisfaction is reflected in the fact that more and more units are being ordered.
Of course, there have been challenges as seals have become more complex. But they are always excellent opportunities for learning and development, Paavo admits.
MECARING has thus evolved over the decades and continues to do so. Automation and seal innovations will continue to pose challenges, but Paavo thinks Extron is ready for the future.
We must stay awake. One important thing is to keep in touch with manufacturers and partners, even though the industry has expanded rapidly. And we need to keep up with competitors and listen to the needs of the market. With our process expertise and Nordic design skills, we will certainly continue to keep pace with the needs of the plastics industry.